Viewing the Invisible, An Insight into the Infrared Thermography Program at Atlantic LNG
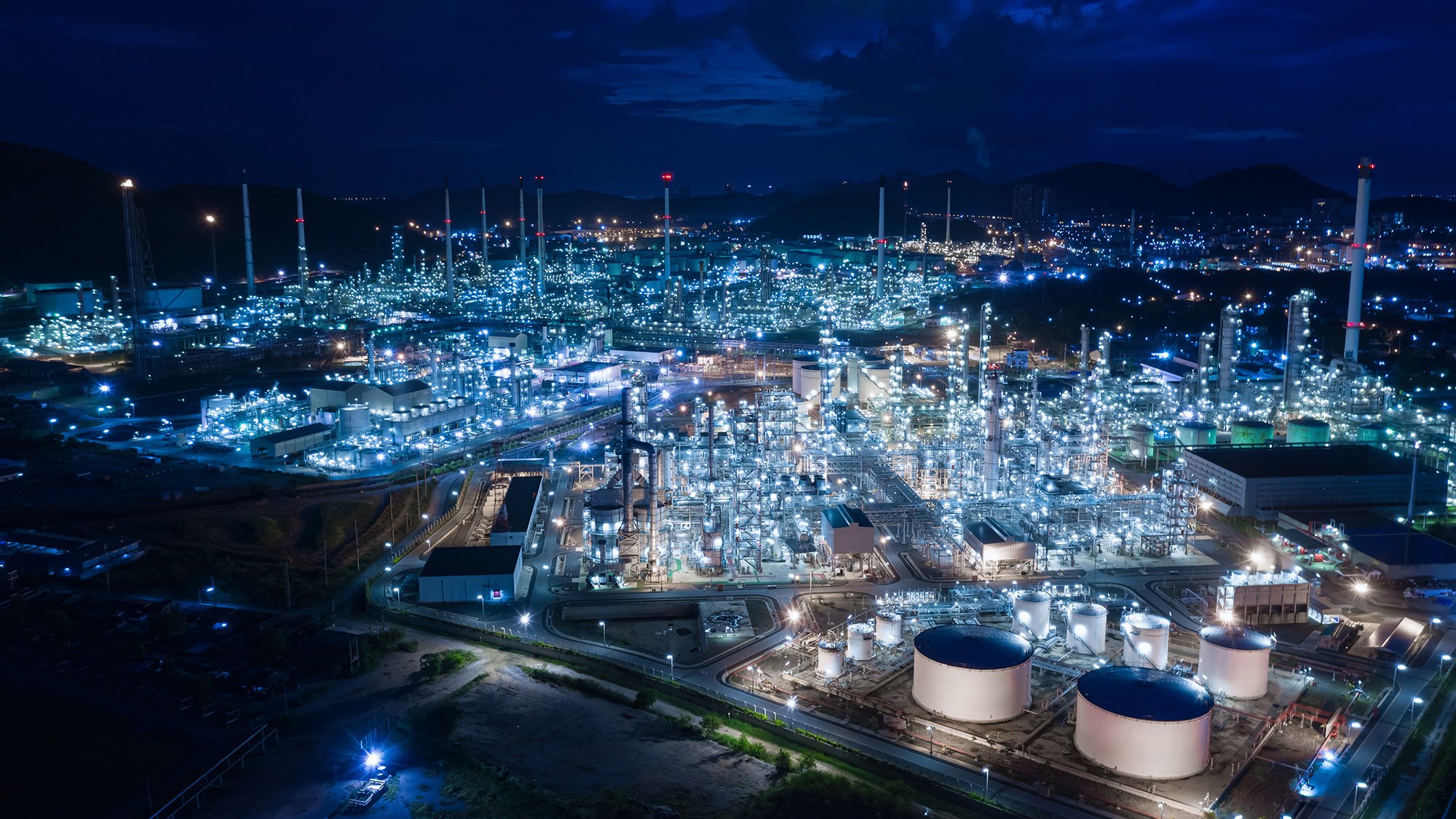
InfraMation 2018 Application Paper Submission
Randy P. O’Rosco, CMRP
Team Lead - Condition Monitoring Atlantic LNG Company of Trinidad and Tobago
ABSTRACT
At Atlantic, we are currently in our 19th year of LNG operations. Increasingly, we are managing and understanding the challenges as a Facility of this nature ages. Discussions were progressed on how we could harness technology to aid us in sustaining safer operations and reducing operating risk. The current Infrared Optical Gas Imaging program is a direct result of this initiative.
INTRODUCTION
At Atlantic, the Condition Monitoring Team utilizes Forward Looking Infrared (“FLIR”) Technology as part of the “Predictive Maintenance Strategy” to provide information on equipment “health” as well as in Hydrocarbon Gas Emission Detection and to aid in effective maintenance management and prevention of equipment failures. Infrared Thermography is a non-contact, non-destructive technology that provides a temperature profile of the equipment being evaluated.
Infrared thermal imagers are a special type of camera that “see” the heat radiated from different types of equipment. Where thermo-grams are in black and white, white is an indication of hot and black, an indication of cold temperatures. If thermo-grams are in color, normally white and red areas are hotter and black and blue areas are colder.
All Condition Monitoring Analysts are American Society for Non-Destructive Testing (ASNT) certified Infrared Thermographers and have also been trained in Advanced Gas Detection which allows for the maximization of the potential application of this technology.
Main FLIR units currently in use are the FLIR GF 320 for Gaseous Emission Detection and the T1K Thermal Imagers used for Mechanical / Electrical surveys. The imagers differ in optics and wavelength sensitivity as well as cost due to the applications for which they have been designed. The successful results that have been realized to date from these imagers have demonstrated that the investment in this technology has been very worthwhile.
BODY OF THE PAPER: PROCEDURE, DATA, CASE HISTORIES, AND EXAMPLES
Infrared at Atlantic Atlantic acquired our first Optical Gas Imager, the FLIR GF 320 in December 2014 for hydrocarbon emissions detection at the facility and trained the Condition Monitoring team in Advanced Optical Gas Imaging.
FLIR was chosen because it is the industry benchmark for quality and versatility when it comes to Infrared Technology. This unit was chosen from the range of gas finder thermal imagers because of the specific gases it can detect and its compatibility with Atlantic’s main refrigerants; Propane, Ethylene and Methane.
The Condition Monitoring Team utilizes infrared thermography for risk mitigation in the applications listed below:
1. Routine condition monitoring on rotating machines
2. Detection of passing valves
3. Blockages in piping systems
4. Detection of loose or damaged electrical components
5. Assessment of transformer condition
6. Detection/verification of levels in vessels and storage tanks
7. Optical Gas Imaging
Initially, the FLIR GF 320 was first used to image high risk areas on the plant to reduce risk as quickly as possible. Structured and systematic Optical Gas Imaging surveys have since been implemented at the plant. It was identified that Methane, Propane and Ethylene emissions significantly increased than before the use of the FLIR technology. The source of the refrigerant emissions that were identified, have been repaired or planned to be repaired and cost savings have been realized due to decreased consumption
Optical Gas Imaging is now also used where there are major Naked Flame Hot Work activities. This has proven to be more effective in detecting emissions than the conventional sniffer detectors thereby reducing the inherent risks associated with activities such as welding and cutting.
Atlantic has also acquired the FLIR T1K thermal imager that provides the ability to perform in-service thermal surveys reducing risk and maximizing plant availability through the ability to plan and execute appropriate maintenance interventions based on thermal information.
Some of the benefits of Infrared Thermography that have been gained by Atlantic have been:
1. Prevention of unscheduled downtime which results improved production efficiency
2. The remote performance of surveys from a safe distance which reduces risk to personnel
3. Improved risk identification and management resulting in reduced insurance premiums
Some key successes to date are outlined in the following examples:
EXAMPLES FROM THE ATLANTIC SITE
Hot Spots were detected on Turbine Exhaust Transition Piece during routine condition monitoring which is an indication of internal insulation degradation. The necessary plans were put in place to have internal inspection performed during a turnaround which revealed a comprised section of the heat shield and insulation. Repairs were performed, and the unit returned to service.
Thermogram indicating passing Pressure Safety Valve (dark colored area on piping downstream of valve). It was found that refrigerants were being lost to the flare system. This represented money being wasted as Propane and Ethylene carry a significant cost. With the use of the thermogram, the valve was repaired and resulted in less refrigerant usage on site with associated cost savings and reduced emissions.
Operations were having problems with flow out of a vessel. There were challenges in locating the actual point of blockage. Infrared Thermography was used, and the actual location was identified. A subsequent backflush was performed, and plant production resumed without having to incur significant losses or downtime.
Thermographic survey on LNG Storage Tank Base Heating System Panels. The thermogram on the left indicates an abnormal hot spot on Electrical Circuit Board. An overheating fuse and cable was located behind the circuit board and could not be seen with the naked eye in the optical image on the right. Corrective action was taken to rectify overloaded condition and prevent failure of the system.
During Infrared Survey on the power transformers at the facility, indications of blocked cooling fins / uneven load was noted on the right side of this unit. This information has initiated further investigative work and plans are underway to have these indications rectified.
An Infrared Survey was performed prior to a planned outage to assist in quantifying the sludge in vessel to aid in planning for internal inspection and cleaning activities.
During a quarterly Optical Gas Imaging Survey, an emission was noted from under insulation of a 0.75” pressure gauge branch piping connection. When the insulation was removed the image on the right, depicting corrosion under insulation – CUI with pin holes in the pipeline, was found and corrective measures implemented.
During routine plant operations a hydrocarbon scent had been reported. The Operations team had challenges finding the source with the conventional gas detectors. The Condition Monitoring Team was contacted and using the FLIR GF 320 Imager, the source was quickly found . It was emanating from an aluminium plate fin heat exchanger on the plant. An LNG train had to be shut down for repairs in this case. The main benefit here was identification of the hydrocarbon leak and prevention of secondary failures.
Reports were made of a suspected flame at base of Flare Tip. We used IR Technology to confirm the source of the flame from a safe distance which guided the isolation of the fuel source preventing flame impingement on the Flare Tip. These images were captured from the plant’s Western Fence line approximately 2000 feet away using a telephoto lens.
SUMMARY
Atlantic’s Infrared Program has yielded exceptional value with improvements in Planning and Scheduling as well as a Reduction in execution time owing to the fact that the information gained allows for the selection of the optimum solution. This has significantly reduced operational risk.
The Infrared Program information is used in the development of the Maintenance Strategy at Atlantic. The information is routinely used in turnaround (TAR) planning. The information from the Infrared Surveys (both Optical Gas Imaging and routine Infrared Thermography) have allowed for the development of appropriate action plans to efficiently perform corrective and repair activities on plant equipment where defects in the past would have gone undetected and may have contributed to extended outages and production losses.
The return on this investment in Infrared Technology, training and equipment continues to increase as the program is reviewed and expanded as lessons learned are applied continuously.
These learnings can be adopted in different industries and can have a significant impact to any organizations’ risk management strategy and ultimately its safety performance.
REFERENCES
The Electromagnetic Spectrum is made up of various wavelengths. Only a small portion of the EM Spectrum is visible to the human eye as seen in figure 1 above. For all other wavelengths (longer or shorter wavelengths) specialized equipment is required to “see” the radiation emitted from objects.
Infrared energy (longer wavelengths than visible light) is seen by using Infrared Imagers and these units are simply receivers that process Infrared Energy and converts it into a thermal image that can then become detectable by the human eye.
ACKNOWLEDGEMENTS
I would like to thank the following Condition Monitoring Team members for their contribution to this paper and the success of the Infrared Thermography Program at Atlantic LNG.
Richard Ramsaran, ASNT TIR Level II
Condition Monitoring Analyst II
Atlantic LNG of Trinidad and Tobago
Yannick Gopaul, ASNT TIR Level II
Condition Monitoring Analyst II
Atlantic LNG of Trinidad and Tobago
Mark Hirst, ASNT TIR Level II
Condition Monitoring Analyst II
Atlantic LNG of Trinidad and Tobago
Adio Williams, ASNT TIR Level II
Condition Monitoring Analyst III
Atlantic LNG of Trinidad and Tobago
Kwesi Antoine, ASNT TIR Level II
Condition Monitoring Analyst III
Atlantic LNG of Trinidad and Tobago
The author would also like to thank the Leadership and Management team members at Atlantic that have supported us in harnessing Infrared technology to enable safer Operations and Risk Management at our site.
ABOUT THE AUTHOR
Randy P. O’Rosco has been a Condition Monitoring professional for the past 12 years. He is an ASNT NDT Level II Thermographer and currently, Team Lead - Condition Monitoring at Atlantic LNG Company of Trinidad and Tobago where he is accountable for the Infrared Thermography program at the 15 MTPA LNG Facility. Randy had a key role in developing the present Infrared Optical Gas Imaging Program at Atlantic and together with his team of Certified Thermographers, brought it to the success it is today. Randy also holds certification as an ISO Category III Vibration Analyst as well as a Certified Maintenance and Reliability Professional.