Five Years of Infrared Results at CNA – March 2005 through June 2010
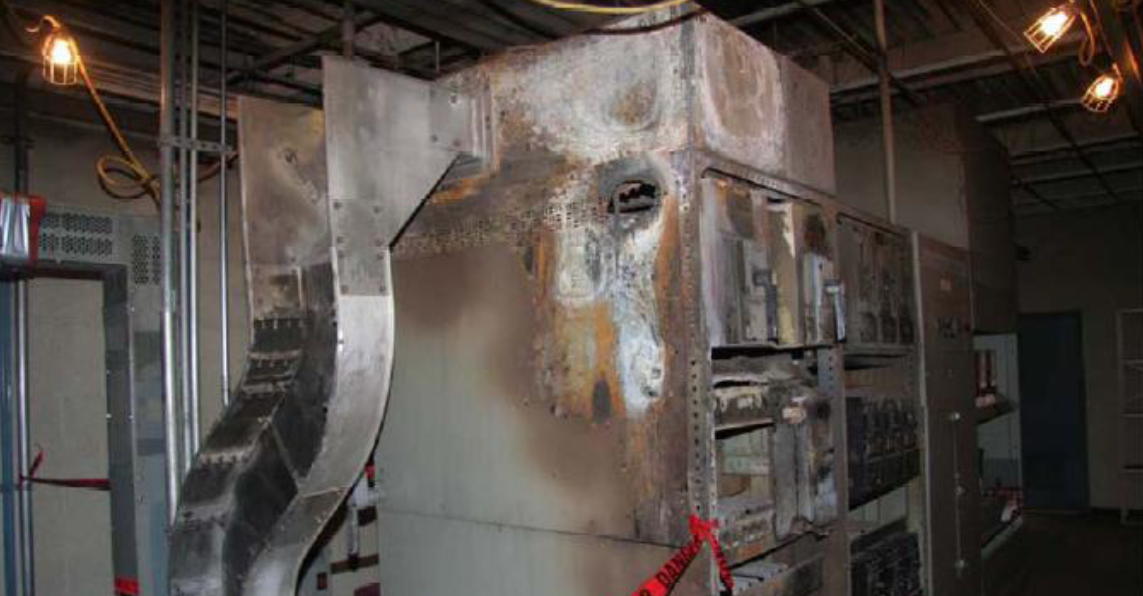
InfraMation Application Paper Submission
IR Thermography Saves Energy and Avoids Losses for CNA Clients
Thomas Gray CNA Insurance
ABSTRACT
Electrical systems – for obvious reasons – are designed to be reliable. Like any complex system, electrical systems require periodic maintenance and inspection to ensure power is supplied to buildings and facilities in a safe and efficient manner. Infrared (IR) thermography can detect heat in the form of infrared energy that is emitted from faulty equipment. Everything with a temperature above absolute zero releases thermal, or infrared, energy. The light composed of this energy isn’t visible because its wavelength is too long to be detected by the human eye. The higher an object’s temperature, the greater the IR radiation it emits. IR thermography cameras can not only “see” this light, but can also delineate hot areas from cool areas.
INTRODUCTION
Insurance companies have traditionally focused on controlling the impact of property losses by using fire protection systems (such as sprinklers) to minimize losses when they happen. Rarely is a service offered that actually helps prevent losses and saves clients real money. IR thermography is such a service. A thermal imaging (IR) scan increases confidence in equipment, decreases the chance for fire loss, reduces energy costs, and helps avoid business interruption losses.
Certified IR thermographers can conduct scans on equipment to find potential problems in the early stages of breakdown or failure. Mechanical systems and key production equipment are also assessed during IR thermography. No interruption of production is typically required during the test. Section 21.17.5 of NFPA 70B 2006 edition recommends that building owners complete IR surveys annually. Other sources recommend every 3 to 5 years, depending on the number and level of faults found, but some recommend every 2 to 3 years.
From March 2005 through June 2010, our thermographers have conducted 6,445 IR surveys, averaging about 100 surveys per month. Using 22 (FLIR P65 model) IR cameras, our thermographers have found 47,077 faults (or deficiencies) for an average of 7.3 faults per report.
Electrical repair cost savings are estimated at $500 for minor or intermediate faults and $3000 for serious or critical faults. These estimates are based on typical industry experience. The four fault categories are based upon temperature differentials from the norm. Minor faults are 1° – 9°F above the norm. Intermediate faults are 10° – 34°F; serious faults are 35° – 74°F; and critical faults are 75°F or greater above the norm.
Energy savings vary by temperature differential and current (amps). Energy savings can be calculated using a FLIR created tool called “Indirect Power Calculations from Surface Temperatures” or estimated from a number of sample calculations and assumptions. The following are considered reasonable estimates – $1.50/day for critical faults; $0.75/day for serious; $0.40/day for intermediate; and $0.15/day for minor. A cost of $0.15 per kilowatt hour (KWH) is used to develop these estimates, but energy costs may be higher in some areas. We use 250 working days in a year (estimating 10 holidays) to estimate energy savings for each fault.
The value of an IR survey is estimated at $2,000-each based on typical experience of our thermographers. That equates to $12,890,000 total value. These IR surveys have “saved” CNA clients an estimated $55 million or about $4 saved for every $1 value of IR survey. These savings include both reduced electrical repair costs and energy savings.
Electrical fire losses are avoided by correcting faults discovered during IR surveys. Insurance loss statistics (from 1992-2001, as published in 2002) showed that “average” electrical fire losses were about $200K for circuit breakers; $500K for switchgear; and $1 million for Motor Control Center (MCC) rooms. A reasonable “average” electrical fire loss in 2010 is estimated to be $750K based on inflation factors (Means cost analysis data) and more recent CNA Insurance loss experience.
The actual chance of an electrical fire occurring is difficult to quantify. We use the “average” electrical loss of $750K or use the specific loss by type (circuit breakers, switchgear, or MCC rooms) for critical and serious fault(s) discovered during the IR survey. We do not calculate or estimate fire losses for intermediate or minor faults. If the fault is found on specialized equipment (like a transformer), we use specific replacement cost information for the type or piece of equipment.
Business interruption (BI) estimates are based on the percentage of operations lost for number of days (divided by 365). The basic electrical fire risk estimates (above) include both PD and BI loss numbers. We focus on critical and serious faults only for BI estimates, but not every fault will have a BI estimate associated with it. We focus on key equipment (such as transformers or boilers) that has BI potential for plant or facility operations. A reasonable minimum BI loss estimate for critical and serious faults is one day’s loss of 100% operations, but the BI estimates are sometimes more than one day.
HERE’S AN EXAMPLE
A CNA thermographer did an IR survey at a fruit processing facility. The facility had over $20 million TIV including $4 million Contents and $10 million BI value. The CNA thermographer identified one critical, three serious, and ten intermediate faults as a result of the survey. The critical fault (Figure 2) already showed visible evidence of charred insulation (Figure 3). If that fault had become a fire (and it was very close to doing so), the facility might have lost 100% of its contents value due to a smoky electrical fire destroying processed fruit in storage. That is an estimated $4 million loss avoided. The correction of the other faults saved the client an estimated $40,000 in electrical repair costs, energy savings, and value of the IR survey.
The outside/face of the panel was warm to the touch (Sp1). Upon removing the cover, there was immediate odor of burning/melting material (conductor insulation) and visual indications of burning/charring on the panel face. The insulation on the conductors actually showed burning/charring and some of the insulation had apparently melted away. Temperature of the two bottom conductors indicated a temperature of over 407.6°F in Area 1. Sp2 notes a temperature of 182.9°F at the top conductor. Extreme heat and failure of electrical components can result in a fire with ensuing property damage and unplanned interruption of business operations. The plant electrician was contacted immediately to get the fault repaired due to the seriousness / criticality of the situation. A temperature differential of greater than 75°F is considered a critical fault and needs to be repaired immediately by a licensed electrician.
SUMMARY
Our thermographers have identified one or more critical or serious faults on 3,067 surveys out of the total of 6,445 surveys completed so far. If we apply the $750K “average” electrical fire estimate, that adds up to about $2.4 billion in electrical fire losses avoided. Adding BI estimates raises the total even higher. Most of these savings are realized by CAN, but the insurance client also realizes savings from avoiding the insurance policy deductible loss costs.
Since the IR program began in 2005, we estimate that clients whose equipment was scanned by our thermographers have saved more than $13 million per year. IR is another example of how CNA Risk Control works with its clients and agents to help strengthen their risk management programs and integrate services that help protect lives, safeguard assets, and increase profitability.
REFERENCES
MADDING, ROBERT P. “Indirect Power Calculations from Surface Temperatures” tool provided by FLIR.
ACKNOWLEDGEMENTS
The author wishes to thank the FLIR Infrared Training Center (and instructor Jay Bowen in particular) for providing high quality IR training over the past 5 years. He also wishes to thank CNA management for providing the resources needed to make the IR program successful. Last, but not least, he is grateful for the efforts of all of our thermographers who successfully do the IR field work and reports.
ABOUT THE AUTHOR
Tom is a Level III thermographer who has been doing IR for more than 5 years. He is a 1974 Purdue University graduate with an Interdisciplinary Engineering degree. He has 36 years of experience in insurance and risk management.