Developing and Deploying a Successful OGI Monitoring Program in the Upstream & Midstream Oil & Gas Industries
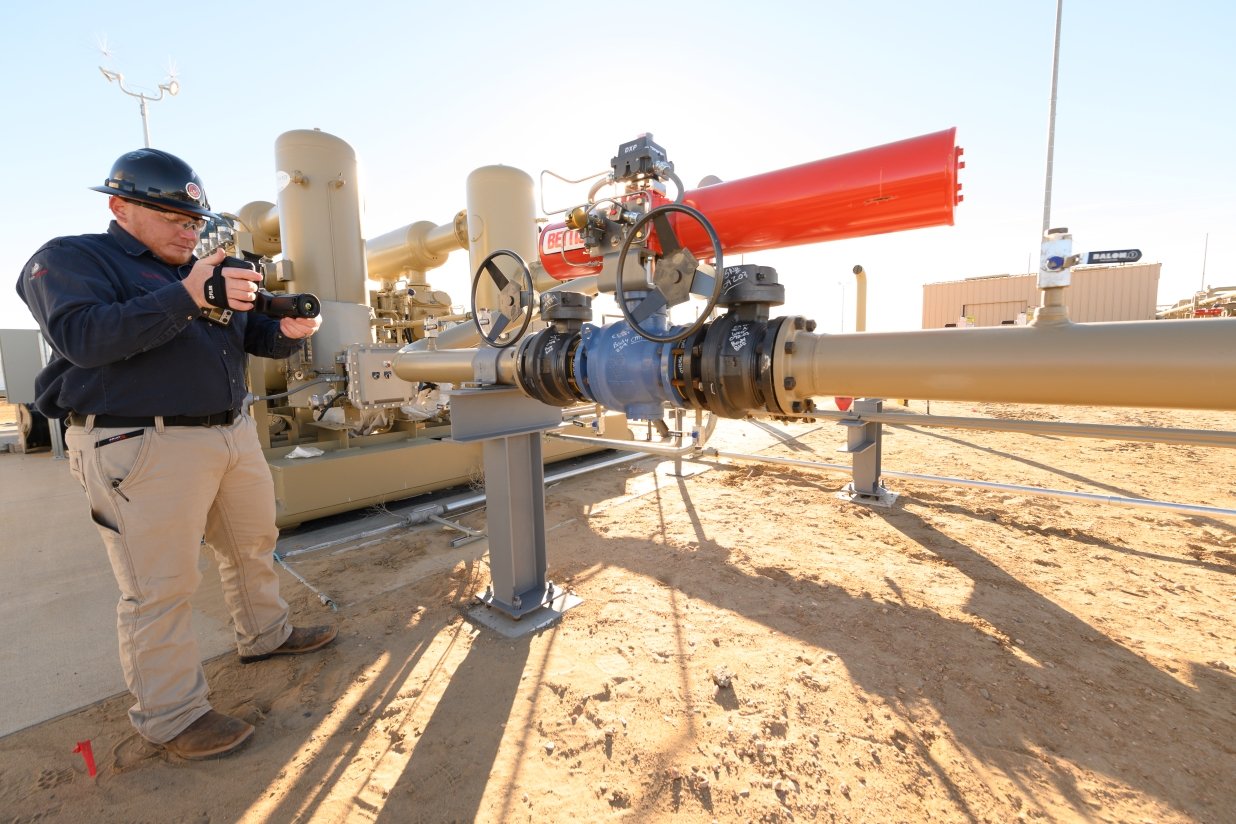
InfraMation 2018 Application Paper Submission
Georgette Reeves
Trinity Consultants
Abstract
Adding to the complexity and confusion surrounding environmental compliance at facilities in the upstream and midstream oil and gas industries are new and often somewhat duplicative leak detection and repair (LDAR) requirements under both state and Federal programs. How can an operator keep track of the multitude of requirements associated with these LDAR programs, and how can these surveys be used to achieve compliance and maximize operational efficiency? Careful planning and a strategically developed LDAR program can address the complexities and practical hurdles that come with such a program. We will cover the key elements of the development of a formal Optical Gas Imaging (OGI) LDAR program, including lessons learned from the development of these programs in the upstream and midstream industry. We will share how operator training can reduce duplicative requirements and streamline compliance; the critical differences between a “leak” and a “vent” when conducting OGI surveys; and how to develop a formal OGI Monitoring Plan that is both compliant with the regulatory requirements and is helpful for ongoing training and compliance.
Introduction
Natural gas is highly adept at remaining undetected, relative to other gases. It is both colorless and odorless, making it often invisible to the naked eye and nose. In order to identify instances of it escaping from pressurized piping and entering the atmosphere, appropriate instruments are required. The technology behind these tools is well established, and for mobile field applications (i.e. physical leak surveys) typically consists of either an optical gas imaging (OGI) camera or an analyzer such as a Flame Ionization Detector (FID). Both of these options allow for the detection of gas that might otherwise go undetected. However, where a FID requires extremely close proximity (i.e. touching) a surface to obtain an accurate reading, the cameras actually visualize the gas stream (which is often invisible to the naked eye) from a distance and make it appear as “smoke” on a screen. One other distinct advantage of this technology is the ability to monitor (survey) multiple components at a time. An experienced team of surveyors properly utilizing the United States Environmental Protection Agency’s (USEPA) Method 21 and an analyzer can survey up to a few hundred components in a day, whereas a single OGI surveyor with basic training can effectively survey several thousand components in the same timeframe.
Regulators have historically taken interest in reducing the amount of gases (i.e. pollution) which enters the atmosphere from industrial facilities. The chemical manufacturing and petroleum refining industries have a long history of applicable environmental regulations which include, among other practices, leak detection and repair (LDAR) requirements. These LDAR requirements have involved utilizing detection instruments to monitor components which were most likely to leak, and repair those found leaking. In more recent years, federal regulations such as the USEPA’s New Source Performance Standards (NSPS) OOOOa1 and state-level regulations such as the Pennsylvania Department of Environmental Protection’s (PADEP) General Permit No. 5 have included requirements for upstream and midstream oil and gas operators to initiate LDAR programs at their facilities. Unfortunately, the implementation of these programs can be a complex and burdensome process. Crossover between complex regulations, training and scheduling personnel across large operating regions, and differences between interpretations of regulations are just a few of the concerns that come with such efforts. However, careful planning and a thorough understanding of the requirements can allow for the process to proceed without issues.
Developing an OGI LDAR Program
Prior to the finalization of NSPS OOOOa, well pads and compressor stations (the two most common types of facilities in upstream and midstream oil and gas operations) were only subject to state-level LDAR requirements, if any at all. These requirements were often quite basic in nature: conduct surveys on a specified frequency with some type of approved instrument, document the results, and fix the leaks within the required timeframes. NSPS OOOOa changed that completely, as all new and modified2 well pads and compressor stations became subject to stringent and prescriptive requirements, particularly related to recordkeeping and survey conditions. NSPS OOOOa is the first round of federal regulation to impact this industry segment allowing OGI technology; while refineries and chemical plants have been subject to LDAR for many years, the waters for OGI compliance remain uncharted and largely without historical precedents. One challenge industry faces is the fact that NSPS OOOOa requires operators to address a number of areas (ex. ensuring an adequate thermal background, or ensuring appropriate distance from leaks based on environmental conditions) which are not explicitly detailed in the regulatory text, thus leaving a great deal of room for various interpretations. How each operator will address these various interpretations should be considered and documented in the required NSPS OOOOa Monitoring Plan. The following sections will outline the main points that should be discussed when developing an OGI LDAR program in the upstream oil and gas industry, as well as lessons learned throughout developing them for a variety of operators.
An OGI Program will have the following elements:
1. Communication and coordination;
2. Documentation (Monitoring Plan and associated recordkeeping);
3. Conducting surveys;
4. Repairing leaks;
5. Planning surveys and trip routes;
6. Tackling the hard to reach places;
7. General safety practices; and
8. Updates to program based on lessons learned.
Each of these elements are discussed in more detail below.
Communication and Coordination
A key element to developing a successful OGI LDAR program will be communication and coordination among a variety of groups of staff: environmental, operations, technicians, consultants and even potential third-party vendors. Although this can often be said for any element of a successful environmental program, it is especially important for LDAR because each of these groups brings their own specific expertise into the picture and can help ensure you are developing a program that is both compliant and reasonable to execute. Coordination and communication can ensure that surveys are completed and documented in a compliant fashion, that repairs are made according to deadlines, that the information necessary for reporting and recordkeeping is gathered, all while ensuring that operations is not distracted from their main purpose (to keep the facilities operating smoothly and profitably). Although each of the following sections must be addressed, this may the single most important take-away from this presentation.
Documentation
At the heart of a solid OGI LDAR monitoring program is a carefully crafted Monitoring Plan, preferably developed with full participation of a variety of stakeholders including environmental, field and facility personnel. Although the level of detail and complexity of these plans will vary depending on their scope (one facility or many) and purpose (e.g., state requirements vs. NSPS Subpart OOOOa), each should clearly spell out how you intend to comply with the underlying LDAR rule(s). This plan should also be a living document, particularly as the industry becomes accustomed to the requirements of the applicable rules. While the plan content can be a simple rule regurgitation (not usually recommended), we have found that with some planning and coordination the Monitoring Plan can be a practical guidebook that any surveyor can implement. The Monitoring Plan should outline the procedures for surveying components, tracking and repairing leaks, and documenting the actions taken. While many of the requirements are spelled out in regulatory text, it is important to think through some of the finer details. For example, if using survey ribbon to mark leaks, what other purposes is survey ribbon used for, and can those purposes lead to confusion when personnel arrive on-site to repair previously marked leaks? Also, the rules require qualified surveyors – it is important to document how you intend to ensure only qualified surveyors conduct surveys. An effective plan is a roadmap that can be easily followed, is based on serious and thoughtful planning, contains the applicable rule’s requirements, and is updated as more surveys are conducted and more lessons learned. Also, a well-thought out Monitoring Plan can be an excellent training tool for new vendors or new hires starting to perform OGI surveys. For operators complying with both state level and federal OGI requirements, the plan could potentially include elements of both programs (which can be very useful as a reference for both surveyors and environmental personnel).
Conducting Surveys
Once a Monitoring Plan has been developed, surveys must be conducted by qualified surveyors that are familiar with the contents of the Monitoring Plan. There are several challenges of conducting surveys:
- Ensuring that all environmental conditions and leak details are properly denoted, including the start and end time of each survey;
- Ensuring that the surveyor knows what is a leak, and what is not
- Finding leaks in unexpected places.
To the first point, denoting all the environmental conditions during the survey is key as it could be difficult (if not impossible) to replicate after-the-fact. Denoting the start and end time of the survey is critical; EPA is keenly interested in the accurate duration of surveys as it is used as a yardstick to gauge whether the surveyor may have been going too fast to adequately identify leaks. As for the second point, this could be one of the single biggest challenges any surveyor will face: when gas is seen in the OGI camera, is it gas being emitted from a permitted vent or stack, is it heat or other interference, or is it a leak? Having clear documentation whenever possible to assist a surveyor in making these determinations can be key in avoiding costly and unnecessary repairs. Keeping detailed documentation on permitted vents can also be helpful should a state or other agency arrive for an inspection; clear and thoughtful documentation that certain pieces of equipment are not considered “leaking” and why can bolster the operator’s case. Apart from knowing which sources are venting and which might be leaks, a surveyor must also be properly trained in general thermography and facility processes. For example, equipment used for the purpose of heat exchange is common at well pads and compressor stations. The surfaces of such equipment may be very hot, and when viewing the equipment with an OGI camera, they may have a shimmering surface which mimics the pattern of a gas leak. However, an experienced surveyor will know that in this scenario, if there is no gas leak the motion will not leave the surface of the hot equipment (will not move away from and be visible against another background), and can easily move on to the next set of components without expending much time on their determination.
Finally, another challenge faced by surveyors are leaks found from unexpected sources. It may be tempting to omit such things as produced water lines from surveys. An initial assumption might be that any components on these lines would not be a potential source of vapor. However, produced water lines still have the potential to leak gas that may be entrained in the water as shown in the following figure:
For those operating in states with state-level LDAR programs, it is not uncommon that both state-level and federal-level regulations apply to a facility, and the required survey frequency may differ between the two. In Ohio, well pads which are permitted under Ohio Environmental Protection Agency’s (OEPA) General Permit 12 (GP12) must conduct quarterly surveys, however a newer pad which is also subject to NSPS OOOOa LDAR would only be required to conduct surveys semiannually. In this case, you can comply with the federal rule (NSPS OOOOa) but still find yourself out of compliance with the state requirement. In order to ensure compliance, these pads must follow the most stringent requirement. In Pennsylvania, well pads authorized under 2013 revision of PADEP Exemption No. 38 must conduct annual surveys. However, if they also have triggered NSPS OOOOa LDAR, the semiannual requirement of the federal regulation will trump the state-level frequency. As such, when developing a program which complies with all applicable requirements, it may save confusion (and potentially an accidental missed survey) to align the survey frequencies to adhere to the most stringent requirement. This, of course, comes at an increased cost, but can increase the operator’s confidence in compliance status (lower potential for agency fines for non-compliance).
Repairing Leaks
A particularly challenging aspect of an LDAR program is the completion of leak repairs. Some state level programs and nonattainment areas may have more stringent repair timeframes than what is found in NSPS OOOOa. Once repaired, the repairs must be verified and documented. Since the personnel making the repair could be separate from the personnel conducting the surveys (who may also be separate from the environmental staff tasked with the LDAR program), the line of communication between personnel needs to efficient and clear. For example: “The elbow on the coalescing filter at the Blue Compressor Station requires repair by April 3rd and John Smith (EHS Manager) must be provided an email confirmation with the repair date once complete. Prior to emailing John, the repair must be verified, which can consist of spraying the elbow with a soap solution and checking for bubbles forming.” From experience, the best case scenario is to have someone on hand who is capable (and authorized) to make the repair on the spot, immediately after detection. This also allows the repair to be verified by the surveyor, and reduces the risk of missed repairs. However, the man hours associated with keeping someone standing by (potentially idle for many hours or even days) result in a monetary and opportunity cost, so it may be necessary to provide those responsible for leak repair a list after completion of the survey(s).
Not every leak can be fixed while the surveyor in on-site, in which case the leaking component should have an identifier attached to it. EPA does not specify how a leak must be tagged for OGI surveys, however it is critical that the tagging procedure is documented in the Monitoring Plan, and the company complies with the documented procedure. Tagging could be as simple as flagging tape, but some state level programs can require component-by-component tagging; any leak that cannot be quickly repaired (or that qualifies as a Delay of Repair component) will need a durable weatherproof tag. Some facilities may opt to track leaking components; while not specifically required by federal rules, tracking leaking components can assist operators with improving the overall design and function of a facility. A spreadsheet is typically the least expensive and most user-friendly option, but can become cumbersome and requires periodic maintenance and will become difficult to manage as more facilities become part of the program. Options such as Environmental Information Management Systems (EMIS) may be too expensive to be justified by LDAR alone, but if already purchased for other program, may also be able to be utilized for leak tracking. LDAR-specific programs such as LeakDAS® are usually geared more towards a Method 21 based program.
Planning Surveys and Trip Routes
Some operators may only have a handful of facilities to periodically survey. In this case, planning a timeslot to complete the surveys is fairly simple. However, other operators may have a hundred individual facilities, all with different operational dates and even on differing survey frequencies. In that case, strategic planning of “windshield time” is a must. Given the remote location of many facilities, weather conditions, and other complicating factors relating to travel, developing a survey completion route based on facility locations with an estimated timeframe will ensure that time is spent efficiently and surveys are completed on time. GoogleEarth is just one tool useful in creating such a route. By saving facility locations into the program, the planner can see a visual representation of each facility’s proximity to the others and develop the route based on that. In this manner, an entire weeks’ route of several dozen facilities can be figured out in minutes.
Tackling the Hard-to-Reach Places (Components)
Although an OGI camera can survey a component from a distance, it does not come without certain limitations. There is a point at which smaller leaks simply cannot be seen, and also areas that electrical devices (such as OGI cameras) must meet certain standards in order to enter. Regarding the former, although it is the experience of the authors that the majority of components can be surveyed without extending beyond the maximum distance that corresponds to the camera’s abilities to detect leaks, exceptions can occur. Also, certain areas of a facility (especially one that processes a flammable gas and volatile liquids), may be off limits to devices that do not meet Class I Division 1 standards under the Occupational Health and Safety Administration (OSHA). These situations present interesting dilemmas to an operator, as components might then fall into the category of “difficult to monitor” (DTM) or “unsafe to monitor” (UTM), which carry with them another layer of complexity in terms of tracking and reporting. The take-away is that there are many unique circumstances which are impacted by specific operator facility configuration and safety requirements, and these must be thought through prior to the start of an OGI LDAR program.
General Safety Practices
Even though the primary intent of most LDAR programs is to ensure regulatory compliance (though in certain cases it may be a best practice or company environmental initiative), the most important element to consider is safety. In addition to being properly trained in conducting compliant surveys, the surveyor(s) must also be trained in conducting safe surveys. When a natural gas company uses their own personnel, this becomes quite simple, as the personnel will likely already be trained in facility operations (what not to touch, what to do in emergency situations, etc.). However, bringing in a contractor to an operational industrial facility changes the game quite a bit. For example, many of these facilities utilize a small amount of natural gas to power process controls, which is then vented to atmosphere. Depending on the piping configuration and the type of controller, this gas may slowly accumulate in a confined area, such as a vapor recovery unit or gas processing unit housing. Even if the surveyor does not physically enter such a space (they may be able to monitor from the outside by looking in), they must know to open the doors and allow the unit to air out, and to check for the presence of gas clouds from a distance prior to surveying from close proximity. An experienced surveyor will have such practices built into their typical procedure, but a novice (even if trained in camera use and thermography) at gas facilities will benefit from specific safety training
Updating Monitoring Plans with Lessons Learned
As surveys are conducted and repairs made, it is important to re-visit the Monitoring Plan to make any necessary updates. As surveys are completed and lessons are learned, it is important to document those important points in the Monitoring Plan such that the knowledge does not become lost in the event of personnel turnover or a change in third-party vendors.
Conclusion
Due to state and federal programs, OGI LDAR requirements are becoming more prevalent for oil and natural gas facilities. Developing an OGI program with multiple stakeholders (environmental, operations, field technicians, etc.) will help ensure a more successful overall program. The foundation of a wellplanned OGI program can be documented in the required “Monitoring Plan,” which can be a living document that can be critical in ensuring consistent survey execution and compliance documentation. Programmatic planning up-front can also streamline compliance requirements between overlapping LDAR programs. Thoughtful planning after program deployment will aid in efficiency for completion of individual tasks. Ultimately, taking time to involve multiple appropriate parties to think through and document the recordkeeping expectations, survey requirements, timeframes, qualifications, tagging and repair procedures, and safety considerations will assist companies in remaining compliant; having a grasp of these concepts prior to contracting with a third-party can also have positive outcomes for all parties involved.
References
Eastern Research Group, Inc.; “DRAFT Technical Support Document. Optical Gas Imaging Protocol (40 CFR Part 60, Appendix K)”; EPA Contract No. EP-D-11-006, Work Assignment 5-09; Revision No. 5; August 11, 2015.
Acknowledgments
Trinity Consultants would like to acknowledge the operators who we have worked with over the past several years. The time that we have spent with them has led to many successful program deployments.
About the Authors
Georgette Reeves is based out of Trinity Consultants’ Austin, TX Office and is the Director of Trinity’s Oil and Gas Sector Services. She has been with Trinity for eleven (11) years, and has broad experience working with oil and gas operators throughout Texas, New Mexico, Colorado, Oklahoma and beyond. She is the course instructor for Trinity’s NSPS OOOOa courses, as well as several Oil and Gas focused courses.